製造メーカーの変更および検品の機械化で
●不具合発生率を低減
●正確な検品および袋詰め作業をセットで実現
課題解決の事例集
小径ナットの不具合と精度が低い目視による検品作業の撲滅
2022.05.06
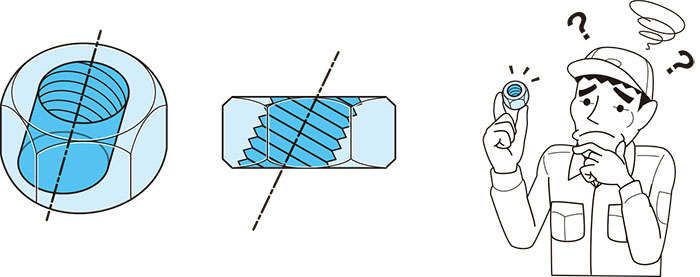
お客様の産業蓄電池メーカー
部署名品質保証
解決策のご提案
相談までの経緯
課題の概要
蓄電池の生産に使用する 小径の真鍮製六角ナットに、“タップが斜めに切られている”という不具合が頻発していた。
やむを得ず後工程で自社内の袋詰め作業があるため、その際に全数の目視検品を実施。
しかしながら月間流動数が多いうえ、小径サイズ(M5径)で視認性が悪いためからか、不良品を続けて流出させてしまった。
やむを得ず後工程で自社内の袋詰め作業があるため、その際に全数の目視検品を実施。
しかしながら月間流動数が多いうえ、小径サイズ(M5径)で視認性が悪いためからか、不良品を続けて流出させてしまった。
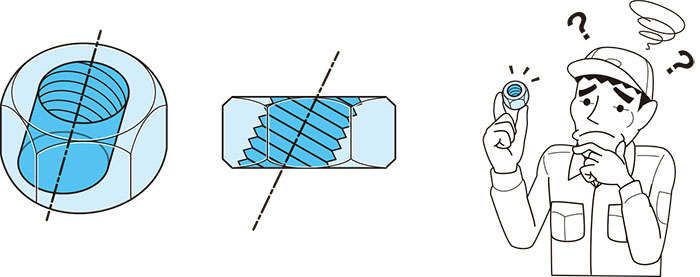
問題の原因
メーカーへ改善要求をするも、品質管理体制が不十分だったために正確な発生原因がつかめない。
調達コストの抑制を最優先した結果、メーカー監査が甘くなっていたことが考えられる。
調達コストの抑制を最優先した結果、メーカー監査が甘くなっていたことが考えられる。
当時のお客様の対策
流出を阻止するため、納入された製品を社内で何度も再チェックしており、時間と手間を考えると実質赤字の案件になっている。
さらに不具合品の混入だけではなく、袋詰め時の員数不足も同時発生していた。
さらに不具合品の混入だけではなく、袋詰め時の員数不足も同時発生していた。
イケキンが提案したこと
課題解決の要件
(1)正確な品質管理が出来ているメーカーを選定すること(発生防止)
(2)袋詰め・検品工程内で不良品を発見できること(流出防止)
(3)社内検品工程を削減し、コストダウンすること
(2)袋詰め・検品工程内で不良品を発見できること(流出防止)
(3)社内検品工程を削減し、コストダウンすること
解決策のご提案 (1)メーカー切り替え (2)袋詰め作業の自動化
(1)ISO9001を取得しているメーカー製品への切替えを提案
自動車関連製品を多数製造しているメーカーA社をご紹介し、同行監査を実施しました。QC工程表を確認しながら、各工程ごとの記録やタップ不良が出ない仕組みなど品質管理体制をご確認いただきました。
(2)画像認識による自動袋詰機での作業切替を提案
ロボットアームと高精度カメラを用いて検品や袋詰めサービスを専門に行うB社をご紹介し、同じく監査を実施しました。
従来の目視検品ではタップの角度をチェックするのが容易ではなく、さらに数万個の小径サイズとなれば、よりヒューマンエラーが発生しやすくなります。B社の自動サービスであれば正確な検品が可能です。
自動車関連製品を多数製造しているメーカーA社をご紹介し、同行監査を実施しました。QC工程表を確認しながら、各工程ごとの記録やタップ不良が出ない仕組みなど品質管理体制をご確認いただきました。
(2)画像認識による自動袋詰機での作業切替を提案
ロボットアームと高精度カメラを用いて検品や袋詰めサービスを専門に行うB社をご紹介し、同じく監査を実施しました。
従来の目視検品ではタップの角度をチェックするのが容易ではなく、さらに数万個の小径サイズとなれば、よりヒューマンエラーが発生しやすくなります。B社の自動サービスであれば正確な検品が可能です。
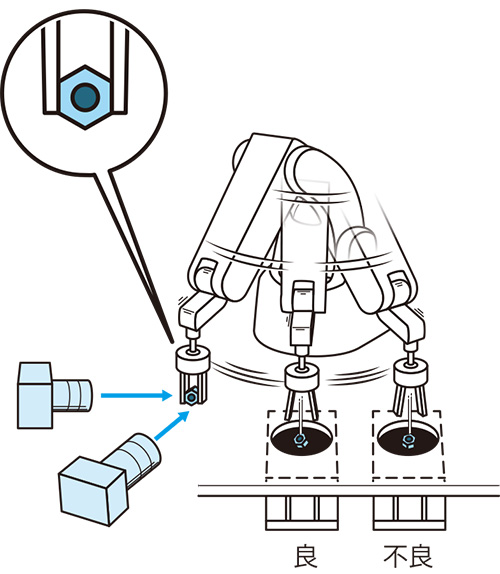
技術検証
(2)画像認識による自動袋詰機メーカーの監査を実施
タップが斜めに切られた製品を混ぜた状態で検査を実施したところ、すべての不良品が検出されました。
タップが斜めに切られた製品を混ぜた状態で検査を実施したところ、すべての不良品が検出されました。

対策の成果・結果
提案結果
2社のメーカー監査後、工程変更が認められてから製品不良は発生していません。また袋詰め時の員数不足という別の課題も解消されたようです。
お客様の調達原価は上がったものの、人件費や損失の補填を差し引くとトータルコストダウンに貢献しています。
お客様の調達原価は上がったものの、人件費や損失の補填を差し引くとトータルコストダウンに貢献しています。
ユーザーメリット
(1)製品品質は上がり、トレーサビリティが取れるようになった
(2)袋詰めおよび目視の自社内工程を削減できた
(3販売後の不良対応をすることがなくなった
(2)袋詰めおよび目視の自社内工程を削減できた
(3販売後の不良対応をすることがなくなった
同種異サイズ製品(M4)への展開
ビニール袋を色分け(青地と緑地)し識別することを提案し、採用されました。
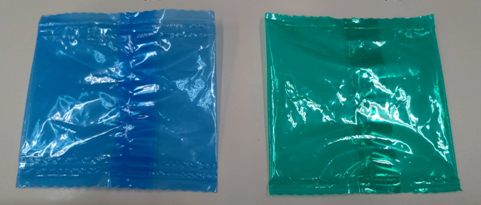
曖昧な内容でも遠慮なくご相談ください!
じっくりお話をお伺いし、解決方法をご提案いたします
・目に見えないコスト(特に人件費)は間違いなく減った。またお客様の信頼を損ねる心配がなくなって気持ちが楽になった。
・繁忙期の残業による社内検品作業が無くなり、在庫管理のみで済むようになった。